Quality Certification: Elevating Our Commitment to Excellence
We dedicated our company to excellence, one machine at a time.
Our equipment and factories are meticulously crafted and certified to leave an indelible mark. From the first sip, we make the quality taste good.
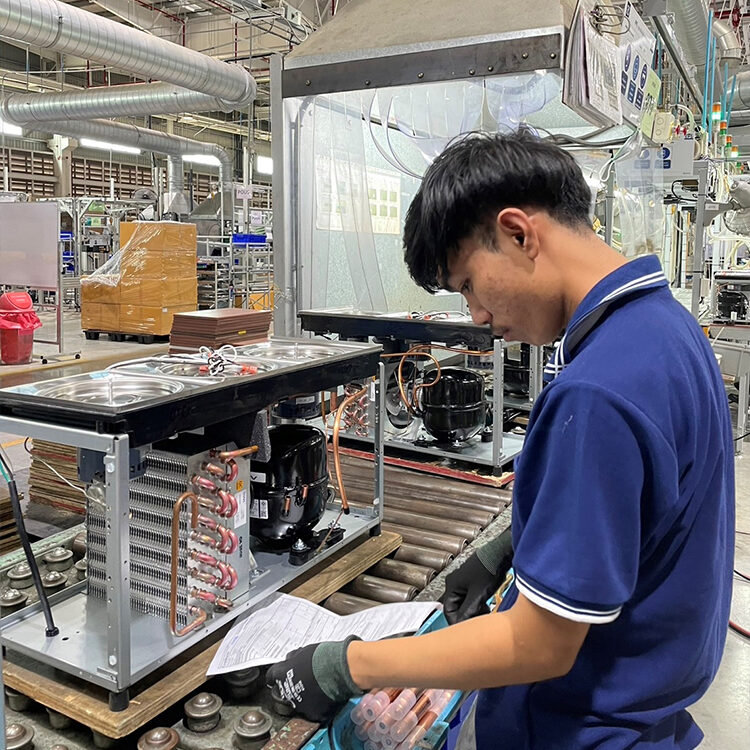
CRATHCO Drink Systems: Where Quality and CSR are Certified.
- ISO 9001: This quality management standard is a testament to our relentless focus on customer satisfaction and continuous improvement. At CRATHCO, this certification is brought to life through our rigorous quality control checks at every stage of production and our systematic approach to addressing customer feedback, ensuring that every product not only meets but exceeds customer expectations.
- ISO 14001: Demonstrating our dedication to environmental stewardship, this certification underscores our efforts to minimize waste and reduce environmental impact. We achieve this through initiatives such as our advanced wastewater treatment processes and our use of a Building Management System (BMS) in our factories.
- ISO 45001: Safety is paramount at CRATHCO, and this certification highlights our focus on creating a safe working environment. We enforce strict safety protocols and conduct regular employee training on health and safety practices, ensuring a workplace that not only promotes well-being but also actively prevents accidents and injuries.
- ISO 50001: Energy efficiency is key in our operational strategy. This certification reflects our efforts to reduce energy consumption across our facilities through the use of energy-efficient technologies and ongoing energy usage assessments to continually improve our energy management practices.
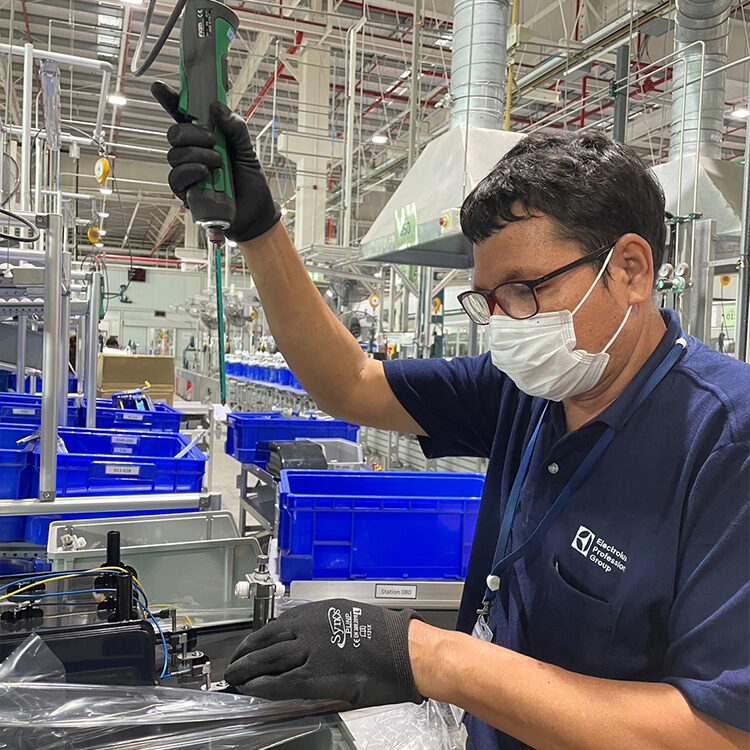
CRATHCO Factory: Where Quality and Craftsmanship Converge
Our production line is a symphony of advanced automation and meticulous craftsmanship. Enhanced by an IoT system, our process not only ensures each dispenser meets our high standards but also embodies our commitment to efficiency and consistency. Rigorous safety tests, gas leak checks, and continuous quality control are integral to our manufacturing philosophy, ensuring every unit is built to last and performs flawlessly under any conditions.
We continually innovate and refine our processes to manage resources effectively. CRATHCO isn’t just about manufacturing beverage dispensers; we engineer experiences that promise quality, innovation, and sustainability with every pour.
But what’s in it for you?
- Peace of mind: Our certifications guarantee that our machines are not only safe and reliable but also compliant with essential health and safety standards. Bid farewell to concerns about whether your machine meets the required standards – we’ve got that covered!
- Simplified compliance: Navigating the intricate landscape of industry regulations and standards can be overwhelming. That’s why we’ve taken the burden off your shoulders. With our certified machines, you can confidently ensure that you’re meeting all necessary criteria, maintaining a solid legal standing.
- Cost Cuttings: Keep your cash where it counts! Our machines are designed to minimize downtime and reduce repair costs, ensuring your budget flows as smoothly as our beverages.
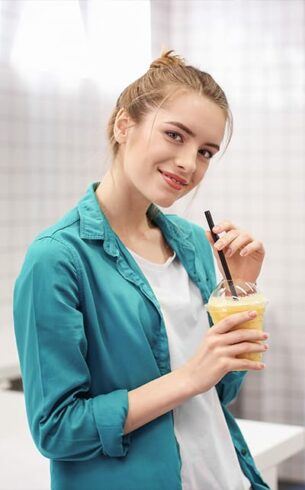